
The Delaware countryside is dotted with poultry houses, some new, some very old, but all ubiquitous and symbolic structures of the Delmarva broiler poultry industry, which supports a significant portion of Delaware agriculture’s $10 billion annual economic impact.
An estimated 2,400 houses lie vacant from the early era of Delmarva poultry’s boom. About half are pre-WWII era and in various levels of dilapidation. Each, longer than a football field, collectively add up to a conservative 700 acres, about twice the size of the University of Delaware’s College of Agriculture and Natural Resources campus in Newark.
Owners of these homes face a challenge: repair, remove or renovate. All of the options are costly, and few are practical. The land under a poultry house, for instance, cannot be returned to production without costly soil remediation.
Instead of collecting cobwebs, what if these structures can produce something sweet and nutritious?
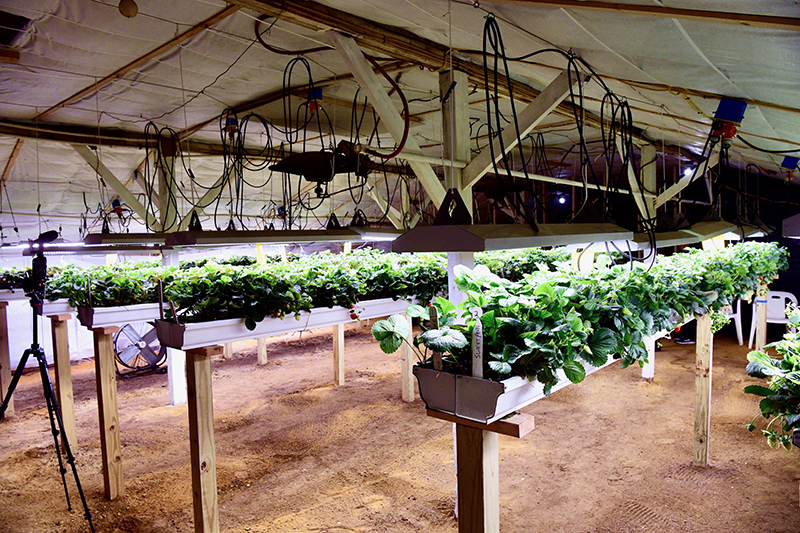
In Roxana, Delaware, farmer Bill Owens is optimistic. He envisions growing fruits and vegetables inside an older stick-built structure on his farm. If he can make it work, he hopes to inspire other farmers to do the same.
“This is potential for growers no longer in the poultry business to repurpose older houses. It is a viable way to earn a diverse income,” Owens said. “It could be a home run. It could change everything. There’s a lot of potential for tomatoes, peppers, cucumbers, eggplant, etc. But more research is needed.”
For both research and implementation, he turned to UD.
For several years, Owens approached Gordon Johnson, then serving as the fruit and vegetable specialist for UD’s Cooperative Extension based at the Carvel Research and Education Center in Georgetown. Owens wanted to convert a 50-year-old poultry house — 32 by 400 feet— into a space for plant-based food production. Johnson politely waived Owens off, concentrating on his UD research projects. But soon after Johnson’s retirement in 2023, he had both the time and curiosity to collaborate.
Johnson was no stranger to questions about old poultry houses. His UD doctoral research examined the quality of soil once a poultry house was demolished. He looked at a variety of soil remediation techniques before an area could return to crop production. Through the research, Johnson connected with many poultry growers in the industry and projects that might offer cost-sharing programs.
“Most people are looking for grants,” he said. Not Owens. “Bill had a vision of growing produce in a lighted house.”
Johnson knew it would be expensive. Owens offered his own funds.
With UD support and expertise, his vision became a reality.
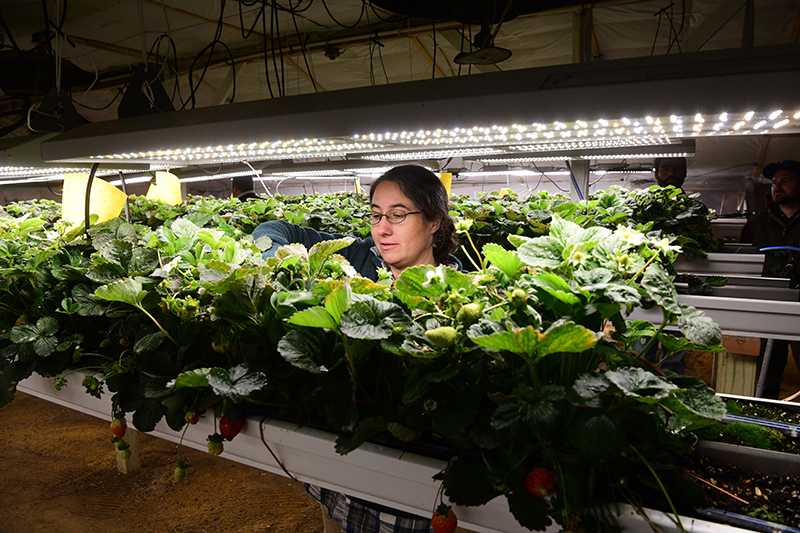
Repurposing vintage houses
First, Johnson helped Owens obtain two grants: one for strawberry production from the Northeast Sustainable Agriculture Research and Education and another from the Delaware and United States Departments of Agriculture to help propagate (or breed) strawberries.
With an initial renovation cost of $69,000, Johnson estimates the total conversion of an indoor hydroponic system, including all equipment and crops, at $251,000.
Johnson’s colleagues in the UD College of Agriculture and Natural Resources provided valuable expertise.
Kali Kniel, professor of microbial food safety, helped ensure that Salmonella was not an issue. For plant-based food production, the space had to be clean, watertight and secure enough to support insulation and electric fixtures. All traces of poultry litter were removed, and although the crop would be elevated in an array of residential gutters, the soil floor, walls and surfaces were tested for Salmonella.
Erin Sparks, associate professor of plant molecular biology, offered spectrometer tests for light-emitting diode (LED) lights under consideration. Lighting decisions were significant. Owens led research for LED lights, which represent 75% of the overall project cost. He also consulted with lighting engineers across the country, finding innovative ways to combine systems with an overall goal of finding methods for making lighting affordable for farmers.
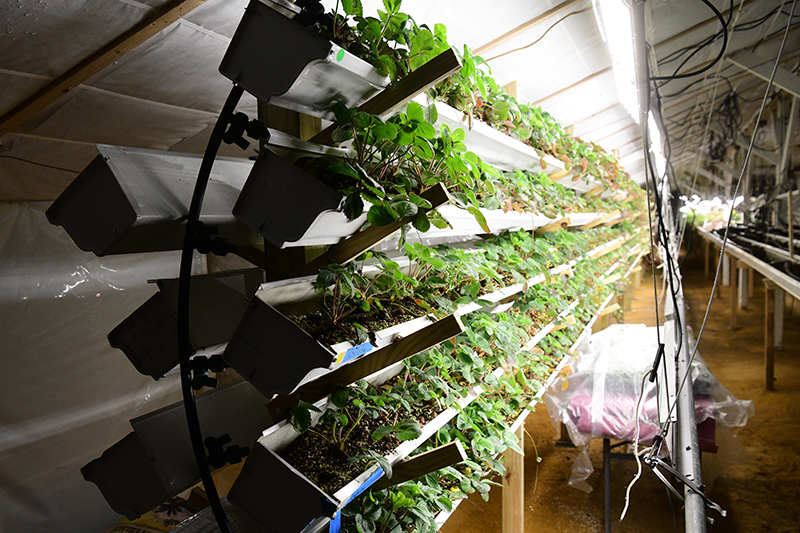
Meanwhile, David Owens (no relation to Bill), a UD Cooperative Extension specialist in agriculture entomology, evaluated common pest management issues and the effectiveness of predator release and commercial products, as well as methods to increase air circulation and timely harvest.
The team also included Jen Jones, extension program assistant, and Owens’ family friend Jen Reed — both providing daily, hands-on care to plants and equipment.
After revitalizing the structure, a process that took just over one year, the team turned to the fruit themselves. Two categories of strawberries were initially considered: June-bearing ones, typically planted in the fall and bearing strawberries in summer, and day-neutral ones, which produce a continual crop for several months. They decided on the latter.
Several cultivars of strawberries grew under 12 to 14 hours of light during evening hours to help keep the interior temperature cooler.
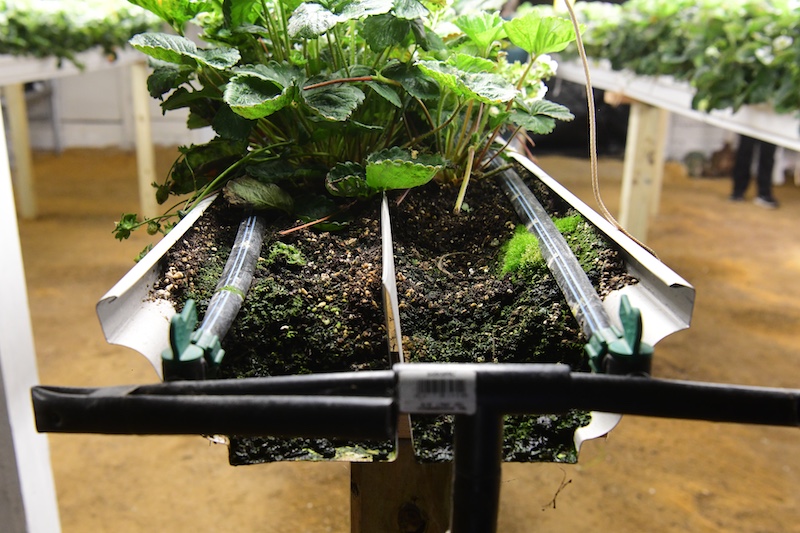
Initial observations
The team experimented with growing media, settling on a combination of coconut fiber, peat and perlite, and looked into options for watering and drainage.
Strawberries performed better when the interior temperature was maintained at 65 degrees Fahrenheit. Day-neutral strawberries performed better, and of the many named varieties tested, “Royal Royce” and “Cabrillo” topped the yield and taste tests.
The clear winner, however, was not the specific strawberry cultivar but rather the plant’s natural propensity to propagate itself. Inside the house, the growth of new tips went into overdrive. Johnson and Owens saw the potential.
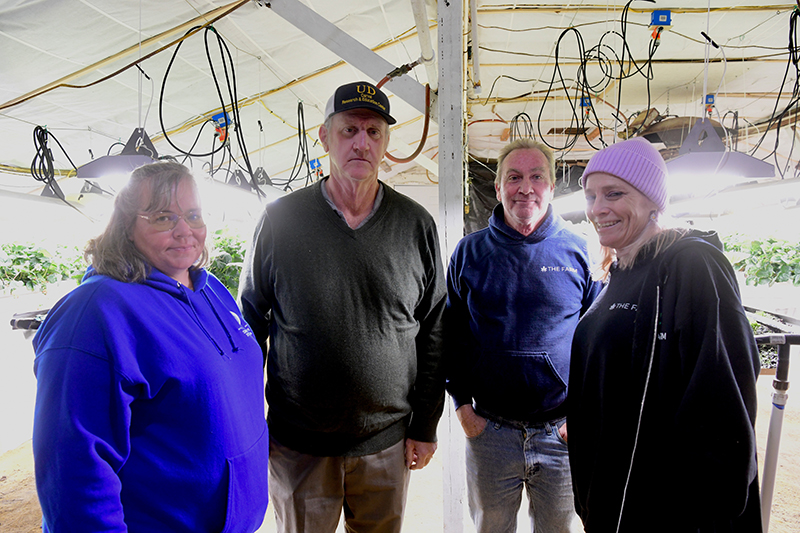
Propagation versus production
Strawberries naturally propagate by runners and need continual thinning out to increase airflow and not crowd the original plant. New tips were emerging at a rapid rate.
Commercial strawberry farmers receive their tips or strawberry plugs from two main wholesalers located in Canada and North Carolina. Recently, North Carolina dropped out as a supplier, leaving a significant void in the supply chain.
Owens equipped the remainder of his house’s space for tip production and arranged the gutters vertically, requiring fewer lights. Johnson estimates converting a poultry house for tips at $171,00, or $34,200 amortized across five years. Supplying tips would earn a five-cent premium per tip for farmers.
“The method of strawberry production underway requires more research,” Johnson said. “But tip production to supply local greenhouses requires a shorter production schedule, less energy and labor. It could be a profitable enterprise for farmers.”
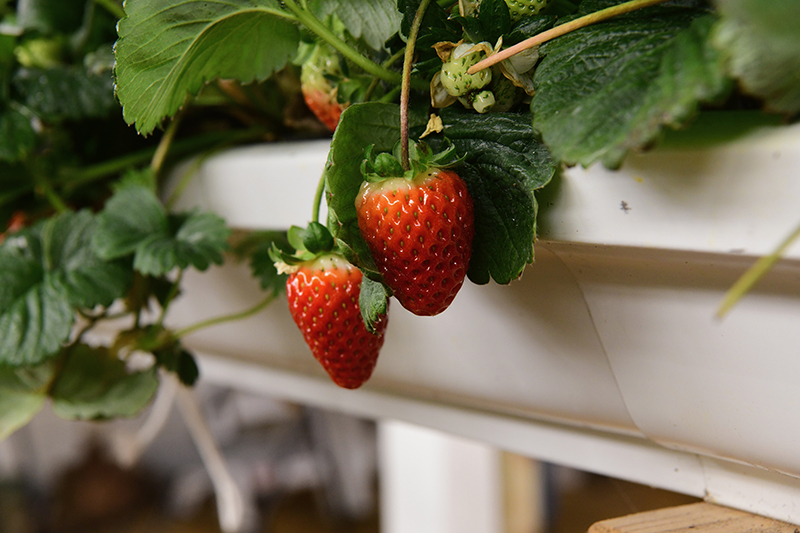