
Like other businesses, poultry production faces challenges, including cash flow, inflation, economic downturns, and market volatility. Despite all those constant challenges and variations, poultry businesses remain profitable. However, it is always necessary to adopt methodologies to optimize productivity and profitability.
Common advice to maximize productivity, profitability, and economic sustainability is to improve efficiency, reduce waste, manage costs, review pricing, and improve infrastructure in the long term.
- Improving environmental sustainability is also related to reducing waste, emissions, and energy use.
Feed is the most important factor affecting production costs and sustainability structures worldwide.
- The most effective method to reduce feed costs is through feed formulation.
- Least-cost feed formulation based on linear programming reduces costs but does not consider maximizing business profitability.
ISSUES WITH LEAST-COST FEED FORMULATION
Least-cost feed formulation has also consolidated the idea that nutrient levels are fixed, obtained from Tables or Breeder Guides, making them an absolute requirement.
- Those “nutrient requirements” for poultry are values determined for maximum biological performance in multiple independent experiments. This means that a maximum of three nutrients have been determined under similar conditions.
- Still, profit-maximizing energy and nutrient levels are only known once an econometric analysis is made for each market and production site.
The most profitable nutrient levels could be variable, depending on changes in feedstuff cost and price of the poultry products to sell (live birds, carcasses, cut-up parts, eggs in shell or egg mass).
A common issue with least-cost feed formulation is that when the prices of protein sources like soybean meal rise, the mathematical solution tends to reduce dietary amino acid density to obtain cheaper feed.
- However, broilers are sensitive to amino acid intake.
- At lower amino acid levels, they may dictate a lower growth rate, yield, higher feed conversion ratio, and lower income, reducing profitability.
On the other hand, profitability may be reduced if the same dietary nutrient density is maintained when the poultry final product price reduces. Bird stocking density and final market weight can also affect the optimum dietary nutrient densities to maximize profitability.
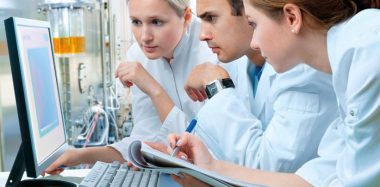
ALTERNATIVES TO LEAST-COST FEED FORMULATION
Instead of looking only at the least cost, a more appropriate approach is to apply feed formulation to maximize profit. Feed formulation to maximize margin or profit can employ nonlinear programming, computer models linked to optimizers, or a combination of both systems.
- Nonlinear programming allows for the inclusion of profit equation(s) instead of a fixed desired nutrient density.
- This means the desired nutrient levels are determined at the time of feed formulation instead of using pre-established “nutrient requirements.”
The profit equation can be obtained by fitting a quadratic curve between feeding cost per unit of gain or income over feed cost versus energy, nutrients, and ingredient levels. These curves are fitted to obtain the function that will produce the economic optimums as energy or nutrient levels vary. Quadratic equations can be used, but other mathematical functions may be more appropriate or accurate to fit this experimental and econometric data.
- This methodology requires obtaining data on animal responses to each energy, primary nutrient, and even main feed ingredient levels.
- However, these responses vary with environmental conditions and, over time, with the evolution caused by constant genetic selection.
- Then, obtaining information from classical dose-response experiments is not sustainable anyway.
Dadalt et al. (2015) compared linear and nonlinear formulations to feed broilers stocked at two densities. A high stocking density (HDH) with 14 chickens/m2 and a low density (LDH) with 10 chickens/m2 were evaluated. Both formulation systems promoted similar broiler performance. However, the high-density feed using linear formulation reduced body weight in 42-day-old males, but not when nonlinear formulation was used.
- The non-linear feed formulation at LDH yielded the highest feed conversion ratio values and the lowest cost/kg broiler for both sexes.
- The results demonstrated that the feed formulation system that yields the best performance or lowest feed conversion ratio is only sometimes the most profitable.
Almeida et al. (2019) also evaluated the value of non-linear programming for laying hens under three market scenarios. They compared it with diets formulated with linear programming following nutrient requirement recommendations of the Brazilian Tables, the genetic strain guidelines, or mathematical models to maximize performance.
- These feed formulation systems did not influence Haugh unit, albumen height, or external egg quality parameters.
- However, feed formulation affected yolk weight, albumen weight, yolk color, yolk percentage, albumen percentage, and performance parameters.
The results of these effects will not be discussed here due to the space available, but in general, feeds formulated using linear programming based on nutritional requirements obtained by mathematical models and the genetic strain manual promoted better performance results because these feeds were nutritionally denser.
However, the treatments or feed formulations that maximized live performance did not result in higher profitability. The maximum profitability was obtained with the diet formulated for a favorable market scenario using non-linear programming, which generally maintained the maximum profitability under each condition.
In conclusion, non-linear programming is a tool to maximize profitability.
- However, data is required to calculate the bird’s response to energy and nutrient levels under diverse conditions, making it difficult to obtain most of the time by empirical observations or experiments. These estimations can be obtained with mathematical models.
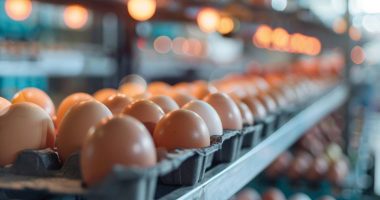
NUTRITIONAL MODELING IN POULTRY NUTRITION TO MAXIMIZE PROFIT
A few academic research groups and several private companies, such as NOVUS International, Cargill, Aviagen, and Trouw Nutrition, have proposed multiple models. Many of these models are not longer available due to their low industry adoption or because they were not updated.
Table 1 shows a comprehensive but not exhaustive list of the published mathematical models that were or are publicly accessible and have implications for poultry nutrition optimization.
- Some models use a series of equations based on empirical research obtained with large datasets.
- In contrast, other models are mechanistic based on theory and research designed to estimate nutrient utilization and deposition parameters instead of only observing animal performance.
- Some of these models included an econometric component or module seeking to optimize profitability and minimize environmental impact rather than only maximize animal performance.
One of the main issues that has limited its implementation, validation, evaluation, and further development has been the need for more education on model development and utilization for practical nutritionists.
The limited understanding of these models’ principles and solid scientific basis comes from the narrow visualization of the multitude of disaggregated scientific publications throughout several decades without references to link them to particular model development.
- Models based on empirical research or collection of observations without seeking explanatory factors have become outdated and underutilized.
- Mechanistic models that describe the main factors causing a response continue to be developed and can be used with the new genotypes while improving prediction accuracy.
Most mechanistic models currently are fixed or employ a single average value, representing the average bird in a group. Stochasticity or potential variability is implemented by simulating multiple times the potential distribution of the population or by altering the most significant factors causing variability.
- The EFG Software and the AVINESP models are two of the most well-developed models.
- These models share similar theoretical or conceptual aspects but differ in some estimation methodologies and terminology.
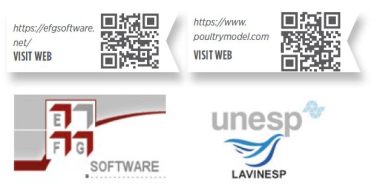
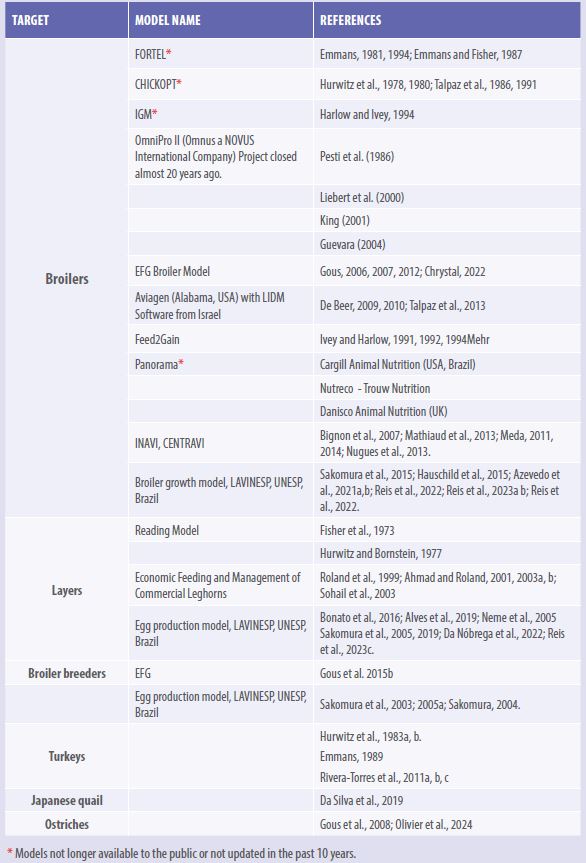
Gerry Emmans, Colin Fisher, and Rob Gous from South Africa developed the EFG models for broilers, broiler breeders, turkeys, and swine. Currently, only the EFG broiler and pig growth models are available. Dr. Nilva K. Sakomura directed the development of the AVINESP models at the State University of São Paulo in Jaboticabal, Brazil.
The AVINESP models have been developed for several species: broilers, broiler breeders, pullets, laying hens, and quails. AVINESP has broiler and layer models available to the public.
These two mechanistic models are based on the theory developed by Gerry Emmans and collaborators in Scotland.
- This theory suggests that accurate mathematical descriptions of animal genotypes and genetic growth potential are critical to determining energy and nutrient requirements in any animal species.
- Accurate mathematical descriptions of egg production are also crucial for determining nutrients according to the stage of egg production and egg mass.
The EFG and AVINESP mechanistic models were developed with a logical series of modules to predict metabolizable energy (ME), net energy (NE), amino acids (AA), calcium and phosphorus needs to meet growth and egg production targets.
- The equations that describe the utilization of energy and nutrients have been published and described. Examples of their ability to predict optimum levels of amino acids to maximize profitability depending on the market objectives have been published.
- In Figures 1 and 2, readers can observe the differences in calculations to estimate the level of balanced protein required to maximize profitability.
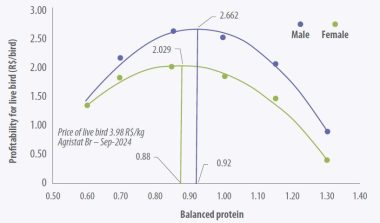

- We still need a better understanding of metabolic processes and efficiencies for nutrient utilization or the impact of other environmental, nutritional, and antinutritional factors and feed additives.
- When using models, it is essential to remember that only the average bird is simulated. The population distribution of the flocks must be included to make the results applicable to commercial conditions.
- Electronic sensor technology, extensive data analysis, and machine learning can improve the accuracy of mechanistic models.
There is a consensus that modeling is more sustainable for conducting poultry nutrition research. It has become a powerful tool for optimizing nutrient excretion and maximizing profitability for more sustainable poultry production.
The 2024 NASEM report on “Nutrient Requirements” of Poultry (10th revised edition) recommended that academia develop mathematical models. However, the NASEM committee report did not address the critical econometric aspect that needs to be included in poultry nutrition.
- Nevertheless, poultry models that the industry could evaluate are already available, as the reader can observe in the information presented here.
- The feedback obtained in the validation of these models can help to improve their precision and accuracy.
- However, adopting these new methodologies for feed formulation in the poultry industry is as critical as developing models.
- Consequently, as previously indicated, more information and education are necessary on this topic, and we hope this article contributes to this knowledge.
Source: avinews.com