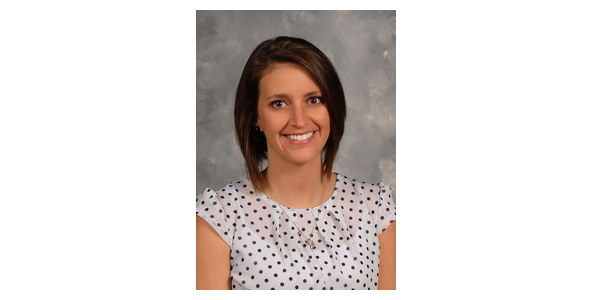
In general, composting poultry can be described as an all-natural, environmentally friendly method of mortality management, which minimizes water and air pollution by retaining nutrients, pathogens, and odors. Given the right conditions, microorganisms break down organic material (poultry mortalities, in this case) and carbon into a useful and valuable finished product. Composting also can enhance disease prevention efforts and biosecurity practices by operating in an on-site, self-contained environment. By mixing the right amount of organic material, an adequate supply of a suitable carbon source (shavings, sawdust, recycled compost material, poultry litter with a sufficient carbon level, etc.), moisture (50 to 60 percent), oxygen (>5 percent with a pile porosity of 35 to 50 percent to allow oxygen to enter the pile), and temperature (130° to 140°F), the composting process works well. In addition, if a temperature of 130° to 150°F can be achieved, this will kill most disease-causing organisms while allowing good bacteria to thrive and continue breaking down organic wastes.
Animal carcass composting began in the poultry industry during the late 1980s, when it was determined that dead chickens could be fully degraded in 30 days (Murphy and Handwerker, 1988). In the 1990s, turkey producers discovered that composting could be successfully used for larger carcasses. Because composting is a relatively simple process that most farmers can easily master, the technique quickly caught on and was rapidly adopted by the commercial poultry industry throughout the “broiler belt,” consisting of the southern and eastern coastal states, where the poultry industry is centered. The process took longer to catch on in northern states because of concerns over its year-round applicability in colder climates (Glanville and Trampel, 1997). There are various methods of composting mortalities, including static bin, alleyway (or channel), windrow, and, more recently, in-vessel or rotary drum composting. Any of these composting methods can be effective under the right conditions, although some may offer more challenges and may take longer than others to complete the process. This article will focus on rotary drum composting of poultry mortalities.
Rotary Drum (or In-Vessel) Composting
In-vessel composting is usually done in an enclosed vessel, such as a large-diameter drum. The material is typically agitated, turned, and/or force-aerated on a daily basis or perhaps multiple times each day, depending on the size of the unit and how it is operated. Because of this daily turning and aeration, the composting process starts quicker and progresses faster in a rotary drum than with static-bin, alleyway, or windrow composting; and the highly degradable, oxygen-demanding materials are decomposed more quickly than with other composting alternatives. There are several rotary drum composters available on the market today, including Biovator™, Ecodrum™, and Rotoposter™, among others. Rotary drum composters, in general, all operate in a similar fashion and offer additional advantages to traditional composting methods: Because they are totally enclosed, there is less chance of leachate escaping; they are quicker and more efficient at material breakdown due to daily turning and aeration; and they use less added carbon source material, such as shavings or poultry litter.
Rotary drum composters have their origin in the swine industry; however, in recent years, the poultry industry has discovered the value of in-vessel composting for commercial poultry growers. Rotary composters are designed for large-scale animal/poultry production facilities and offer the following benefits:
- Reduce odor and disease-causing organisms.
- Eliminate the leaching threat and potential for soil and water contamination.
- Remove animal decomposition from the public eye.
- Enhance biosecurity by enclosing material and removing the scavenger threat.
- Produce finished compost material that has value as a soil amendment.
However, much like static bin, alleyway, or windrow composting, rotary drum composters must have the proper working conditions if they are to perform as intended. Composting requires that you follow a recipe to maintain adequate temperatures and moisture levels and achieve efficient composting results. Within the drum itself, the material must have:
- Adequate moisture content (40 to 60 percent).
- Oxygen (>5 percent).
- Proper carbon-to-nitrogen (C:N) ratio (25-35:1 seems to work best).
- Enough carbon source or bulking agent (shavings, recycled compost, used litter, etc.).
- Correct amount of mortality (do not overload the unit, thereby upsetting the C:N ratio and decreasing the porosity).
- The porosity (or amount of air space within the material) affects the availability of oxygen, temperature, microbial activity, composting time, and the bulkiness and density of the material. It appears the porosity of compost material should be at least 35 percent to facilitate good air distribution and maintain optimum microbial growth. Moisture levels in excess of 60 percent should be avoided because moisture fills up the air spaces within the material, increasing the bulkiness and density of the material and retarding aerobic activity, which reduces the temperature and increases the composting time. In addition, too much moisture can result in the material becoming anaerobic, which increases the likelihood of excess odor generation.
Carcass composting materials typically have mesophilic (grows best in moderate temperatures) and thermophilic (grows best at high temperatures) species of three groups of microorganisms, including bacteria (present in largest numbers), fungi, and actinomycetes (gram-positive bacteria that produce bioactive agents such as enzymes and vitamins) (Kalbasi et al., 2005). Bacteria are faster decomposers than other microbes and usually do well in the early stages of the composting process. Fungi do not do well in low-oxygen environments compared to bacteria; however, fungi are better decaying agents on woody substrates such as shavings, and they are better able to withstand low moisture and low pH conditions. Critical to success is temperature, because nearly all microorganisms in compost material will die if the temperature rises above 158°F, leaving only a few heat-resistant spores. Therefore, it is important that the compost material gets hot enough for the process to work efficiently, but not too hot.
Another useful feature of rotary drum composters is that they do their work out of the public eye. Public acceptance of agricultural practices is an important issue today that every farming operation must take seriously. Public acceptance of a rotary drum composter may be better simply because a drum composter may be more aesthetically pleasing than a bin or alleyway composter. In addition, scavengers are not a problem with a rotary drum composter because all the material is contained inside the drum, preventing scavenger access. With increased awareness of the threat of avian influenza, infectious laryngotracheitis, and other diseases, this can enhance a poultry farm’s biosecurity program.
Rotary Composter on the MSU Poultry Research Farm
The Department of Poultry Science has a rotary drum composter on the poultry research farm at South Farm on the Mississippi State University campus to handle daily flock mortalities (Figure 1). The composter has a built-in thermometer (Figure 2) that allows temperature monitoring on a daily basis. The temperature profile for our unit from May 2014 through October 2016 is illustrated in Figure 3. The composter does a good job of holding 100° to 140°F if we keep enough material in the unit to maintain an adequate critical mass and keep the moisture level in the correct range. Periods when the temperature dropped below 100°F are associated with times when we had the material too wet or when we were out of chickens and we let the unit discharge too much material without adding mortality and it lost its critical mass.
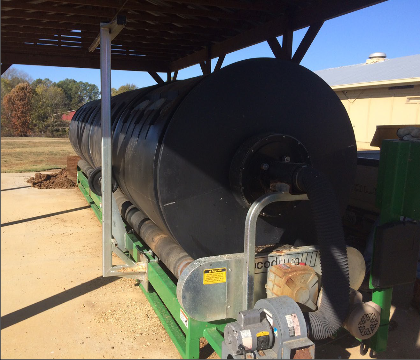
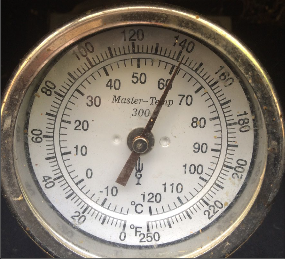

We use pine shavings as a carbon source (Figure 4). Initially, we tried using chicken litter, but our commercial houses have not been totally cleaned out in several years, and the carbon content of our litter is too low to act as a good carbon source. Therefore, we could not achieve the results we wanted. We do reuse a portion of the discharged compost back through the unit, and that seems to work fine if the moisture content is adequate. Manufacturer literature indicates that you can reuse up to 50 percent of the compost exiting the unit. We have a small unit, which consists of two 11-foot drums, 5 feet in diameter, connected to each other. Our unit turns once or twice each day (starting at 6 a.m.), depending on the size of chickens we have on the farm. The grower programs start times and number of turns using the control box on the side of the unit (Figures 5 and 6), and these values can be changed at any time as conditions warrant. The unit turns very slowly, and one complete turn takes approximately 15 minutes and will discharge about half of a 30-gallon trash barrel of material. Two turns will take about 30 minutes and produce a full 30-gallon trash barrel of material.
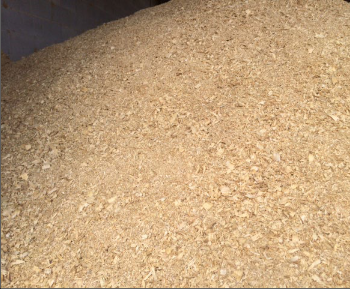
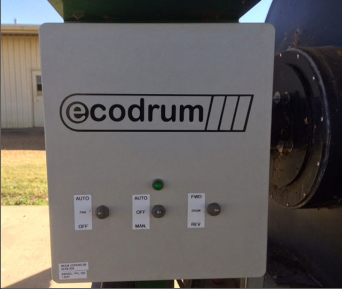

Larger farms may turn their units three or four times per day instead of once or twice and will also need longer units than what we are using at South Farm. Units are sized based on the number of poultry houses on the farm, with additional 11-foot drum sections added to meet the capacity requirements. There are paddles inside the drum (similar to the paddles inside of a cement truck) to help break down the material during rotation and move the material from the front-loading door to the far end of the drum and the discharge chute. The unit also has a blower (Figure 7) that pulls air through the unit on a routine schedule to ensure that there is plenty of oxygen available for the aerobic (oxygen-requiring) microorganisms that break down the material. The drum turns on long rollers (Figure 8), and the unit does have grease fittings (Figure 9) that should be greased once a quarter. You should also check the fluid level in the gear box regularly. Technical support is available to help you determine the initial recipe that works best for your particular situation and to troubleshoot any issues you may have later.
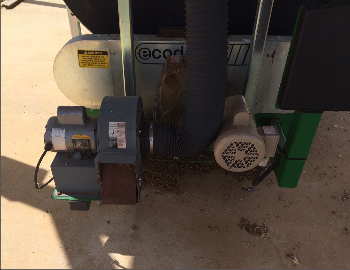
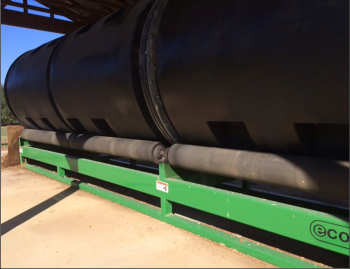
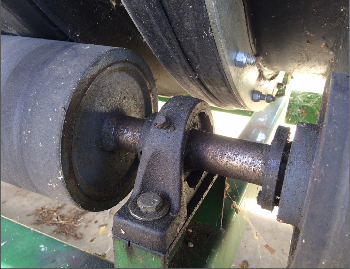
It is fairly easy to observe if the material being discharged is too wet, too dry, or just about right (Figure 10). In our case, material that is too wet is usually very dark and may contain excess moisture. Material that is too dry is often very light. Having material that is too wet seems to be more of a problem for us than material that is too dry. Clumps in the compost are another indicator that there is too much moisture in the mixture (Figure 11). As with all composting, there is a learning curve associated with properly managing a rotary composter, and you must continually adjust the level of shavings or carbon source you add to the composter as the chickens grow. However, the longer you do it, the better you become at determining what the unit needs. For example, while a 1:1 ratio of carbon source to mortality may work fine for young chicks, market-age birds may require a 4:1 ratio or more. You must add enough carbon source to account for all the water that is in the birds or the material will become too wet. Market-age birds have a lot more water in them than baby chicks; therefore, market-age birds will require a lot more shavings than baby chicks to soak up this additional moisture. It is important to recognize that surface area, particle size, and physical properties of the waste material will affect:
- Rate at which composting occurs.
- Types and numbers of microorganisms present.
- Level of biological activity present within the compost material.
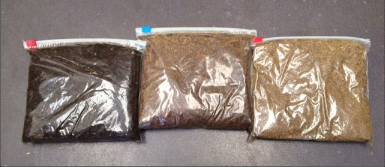
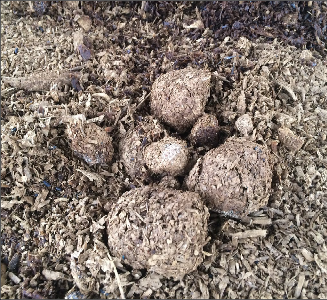
The composting process does allow you to make a mistake and then correct your error. If you mess it up, you can fix it. Very few people have the material too dry. Almost everyone who has problems ends up with the material being too wet to generate sufficient heat. However, adding extra bulking material or carbon source will help dry out the material, and, once it dries out enough, the process will start working correctly. In most cases, the problems are similar for both static bin/alleyway and rotary drum composters. Most growers tend to use too much mortality and not enough dry carbon source to account for all the water in the birds. Once the material gets too wet, it becomes dense and heavy and loses its porosity. When that happens, the material converts from an aerobic to an anaerobic state. Anaerobic conditions yield more odors and flies and lower temperatures. The lower temperatures slow the decomposition process, which can lead to serious problems, such as mortalities being discharged from a rotary composter or remaining in a bin, alleyway, or windrow when the material is turned. Again, composting requires that you follow a recipe. If you don’t follow the recipe, bad things can happen.
You must have access to electricity to power the motor that turns the unit and the one that powers the blower. The 1 horsepower motor that turns the unit requires a 220-volt outlet. The unit has a low cost of operation and requires minimal electrical energy usage because the unit turns only a few times each day. The unit is not designed to load mortalities or carbon source with a front-end loader bucket on a tractor. The loading door on the unit is narrower than the width of most front-end loader buckets.
In Mississippi, the NRCS does have a cost-share scenario for in-vessel rotary drum composting. This scenario has a payment rate of $121 per pound of dead birds per day. The composter has to be placed on concrete and must have a roof covering the structure. The objective of the cost-share program is to provide service to as many producers as possible. Therefore, NRCS has a cost cap on all composting scenarios of $22,950 as of this writing. While the cap may create a problem for many producers, it does allow NRCS to assist multiple producers instead of only a few who may require large funding amounts. Cost-share rates are the same throughout the state, regardless of the number of poultry farms in any particular area.
Similar to bin/alleyway composters or incinerators, rotary drum composters in Mississippi must be permitted by the Mississippi Board of Animal Health (MBAH). The MBAH regulates all dead bird disposal methods in Mississippi. If you are considering a rotary drum composter, contact the MBAH at (601) 832-3351 for assistance with determining the composter size you will need based on your farm size, as well as help with the necessary paperwork.
Summary
Composting is the preferred method of dealing with mortality losses on most commercial poultry farms across the country. Composting offers numerous benefits over other disposal methods, and the final end product is a valuable soil amendment. Rotary drum composters are the newest addition to the composting family. They offer several advantages over static bin or alleyway composting, including reducing odor, eliminating the threat of leaching that would result in soil and water contamination, removing animal decomposition from public view, and enhancing biosecurity by removing the scavenger threat and keeping mortality disposal contained or enclosed. Flies are not an issue if the material stays hot enough (130–150°F) to kill fly eggs and larvae. Lower temperatures may mean flies will be more of a problem. Composting requires that you follow a recipe, which is just as true for rotary drum composters as it is for static bin or alleyway composters. Given the proper conditions, rotary drum composters work well and are a sound alternative to static bin or alleyway composters for dealing with daily mortality losses on commercial poultry farms.